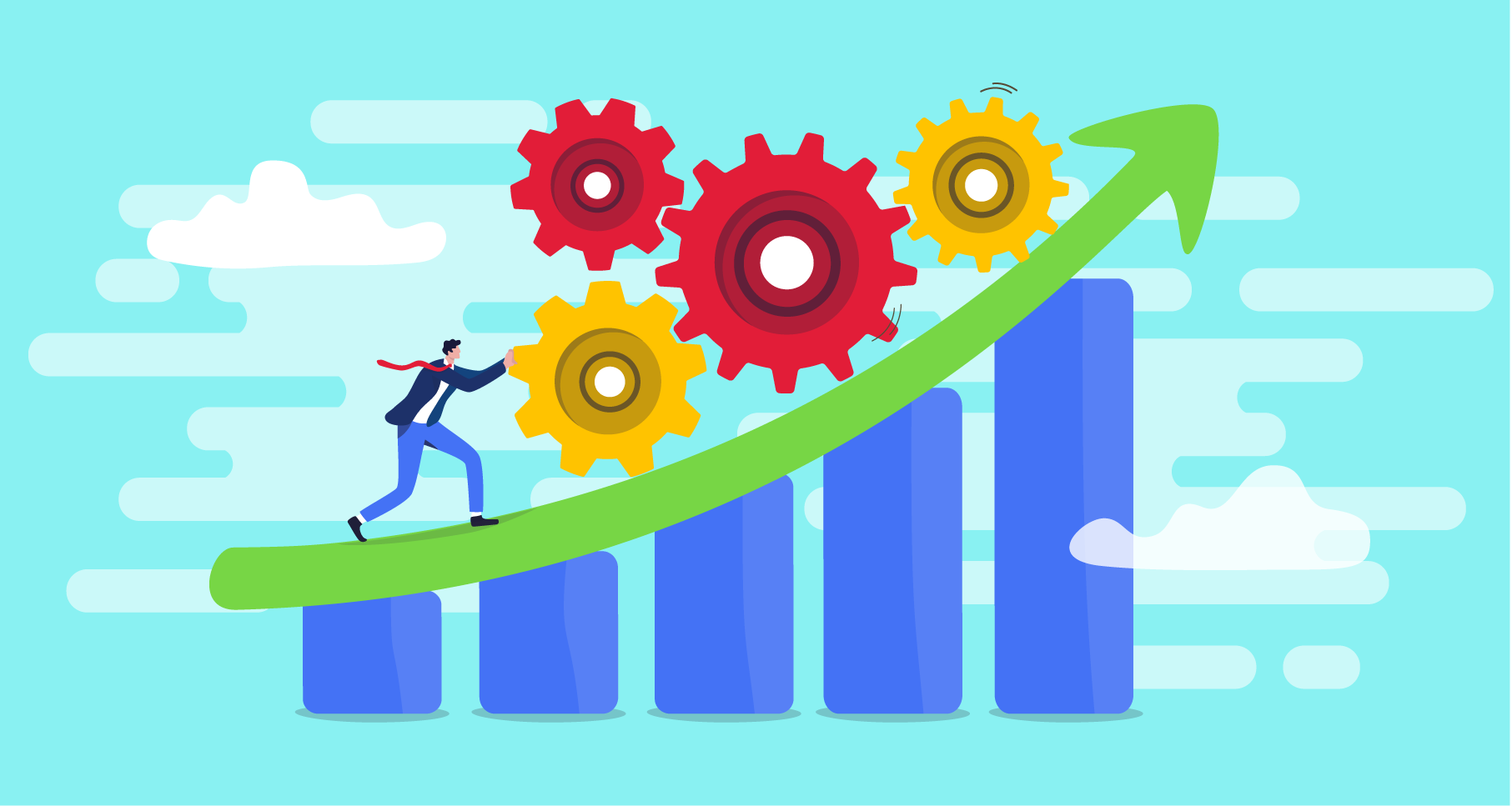
In the era of digital transformation, businesses across various industries are constantly seeking innovative ways to improve their operations and achieve a competitive edge. One such approach is the implementation of a technology-based quality management system (QMS) or simply Quality 4.0. This article explores the benefits of adopting a technology-driven QMS, essential steps for successful implementation, and the key features of an ideal system.
Quality 4.0 is the application of Industry 4.0 digital technologies to improve traditional best practices in quality. This innovative approach can increase productivity and flexibility in the factory and supply chain, with the potential to boost productivity by 10 – 15 percent. By leveraging predictive analytics, sensors, and electronic feedback loops, manufacturers can optimize products, people, and processes while transforming quality strategies.
Quality 4.0 is enabled by digital technology, but transformation occurs when an organization optimizes its products, people, and processes with its technology. It should be deployed as an integral part of a business and/or quality strategy to transform your operations to drive a positive customer experience.
Some examples of digital technology shaping QMS:
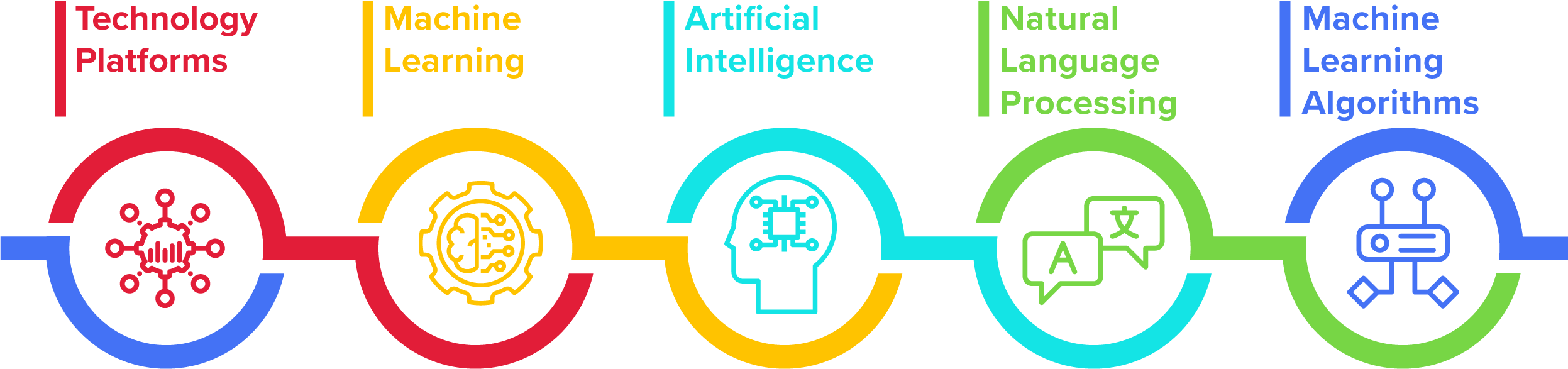
- Technology platforms (TP) such as Veeva Quality Vault, TIPQA, Trackwise, and MasterControl to name a few are getting better and better by incorporating features that you may need.
- Artificial Intelligence (AI) technologies can help reduce manual oversight in manufacturing operations, allowing tighter, proactive control of quality and operating costs.
- Machine learning (ML) can assess manufacturing data across batches and lines to predict quality issues, automate batch release, and optimize yield and output.
- Natural language processing (NLP) can now enable proactive quality management through innovation, addressing key business problems such as volume and staffing challenges.
- Machine learning algorithms (MLA) and AI-based techniques can analyze large datasets to identify patterns and relationships, enabling root cause analysis in manufacturing, customer service, supply chain management, and other fields. Examples of AI-based root cause analysis tools include Tableau, IBM Watson Analytics, RapidMiner, and Logz.io.
The Evolution of Quality Management Systems
The concept of quality management has evolved significantly since the days of the Industrial Revolution, when mass production necessitated stringent inspection procedures to ensure product quality (Hoyle, 2017). Over time, multiple quality management theories have emerged, including Total Quality Management (TQM), ISO 9000, and Six Sigma. The integration of technology into QMS has been a significant change, enabling businesses to streamline processes, enhance efficiency, and foster a culture of continuous improvement (Pitt, 2021).
The Juran Perspective on Quality Management
Dr. Joseph M. Juran, a pioneer in quality management and founder of the Juran Institute, emphasized the importance of quality by design, continuous improvement, and top management commitment to achieving quality excellence. He stated, “Managing quality consists of designing and producing the products and processes required to meet customer’s needs effectively and efficiently as possible.” (Juran, 1992, p. 23). This quote highlights the necessity of aligning an organization’s quality management efforts with customer expectations and requirements. Dr. Juran and our staff’s perspective on quality management underscores the value of adopting a technology-based QMS, as it enables organizations to competently plan, control, and improve their processes to meet customer needs more efficiently and effectively than ever before.
Benefits of Implementing a Technology-Based QMS
A tech-driven QMS offers numerous benefits, including:
- Enhanced data-driven decision-making: Technology-based QMS provides real-time data and analytics, allowing organizations to make informed decisions and facilitate continuous improvement (Chen et al., 2018).
- Improved efficiency: Automating routine tasks and standardizing processes minimizes human error and increases overall efficiency (Terziovski, 2007).
- Enhanced collaboration: Cloud-based QMS promotes seamless communication and collaboration among team members and stakeholders, which is vital for effective quality management (Deshmukh & Hafeez, 2020).
- Compliance management: A technology-based QMS simplifies compliance with regulatory requirements and industry standards, reducing the risk of non-compliance and associated penalties (Becker et al., 2017).
Download the full whitepaper here for a more detailed look at the steps for implementing a technology-based QMS.
Conclusion
Quality 4.0 is revolutionizing quality and manufacturing by integrating digital technologies to enhance traditional best practices in quality. By adopting a holistic approach that encompasses technology, people, and processes, organizations can achieve significant productivity gains and optimize their overall quality strategy. As more manufacturers embrace Quality 4.0, the industry will continue to evolve and thrive in the digital era.
For information on implementing a Q 4.0 System, contact us at [email protected].
About the Authors
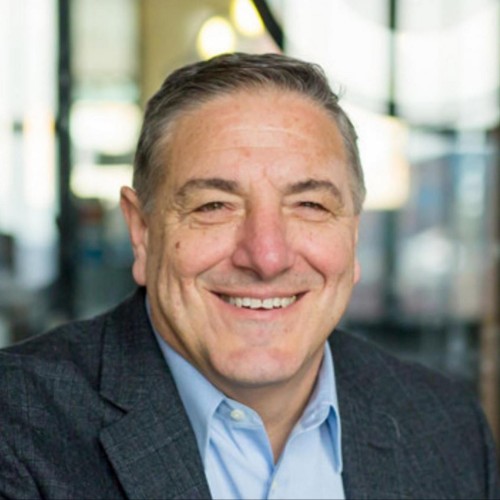
Joseph A. DeFeo | Juran, an Attain Partners Company
Dr. Joseph A. DeFeo has been at the forefront of building cultures of excellence for over 35 years. With a career spanning education, training, consulting, and coaching, Dr. DeFeo has dedicated his life’s work to the pursuit of helping organizations across the globe improve the quality of their people, services, and processes. As one of the world’s leading experts on the development of organization-wide transformation to improve the overall customer experience.
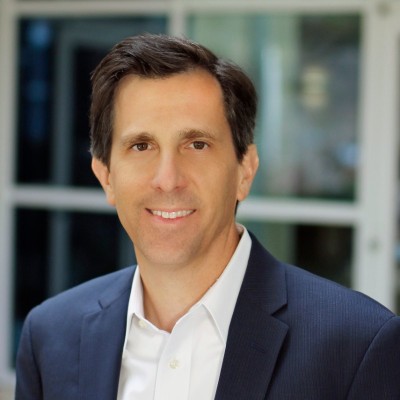
Michael Stamp | Juran, an Attain Partners Company
Michael Stamp specializes in Continuous Process Improvement, Lean Management, and delivering a variety of quality programs to corporate clients. Mr. Stamp has over 25 years of experience and is an outstanding change agent who can identify opportunities, develop focus and provide strategic and tactical business solutions. Mr. Stamp’s core competencies include Process Improvement, Operational Streamlining, Data Science, Special Project Management, Training & Coaching, Cost Reduction, Multi-Site Operations, Quality Control/Assurance, Policy & Procedure Development, Leadership Development & Culture Transformation and Statistics.
References
Becker, J., Knackstedt, R., & Pöppelbuß, J. (2017). Developing Maturity Models for IT Management: A Procedure Model and its Application. Business & Information Systems Engineering, 3(3), 213-222.
Chen, C. J., Wu, H. Y., Wu, C. W., & Chang, Y. C. (2018). Developing a cloud based QMS process assessment model for SMEs. International Journal of Production Research, 56(1-2), 427-439.
Deshmukh, S. G., & Hafeez, K. (2020). Implementation of quality management systems and performance measurement: An empirical investigation. International Journal of Quality & Reliability Management, 37(3), 417-437.
DeFeo, J. and M. Stamp (2023). 2023 Organizational Excellence: Are Ready for Quality 4.0? Online webinar. Attain Partners LLC.
Hoyle, D. (2017). ISO 9000 Quality Systems Handbook – updated for the ISO 9001:2015 standard: Increasing the Quality of an Organization’s Outputs. Routledge.
Juran, J. M. (1992). Juran on Quality by Design: The New Steps for Planning Quality into Goods and Services. Free Press.
Pitt, M. (2021). Quality Management in Construction: A Comprehensive Guide for Project Managers. Routledge.
Terziovski, M. (2007). Building Innovation Capability in Organizations: An International Cross-case Perspective. World Scientific.
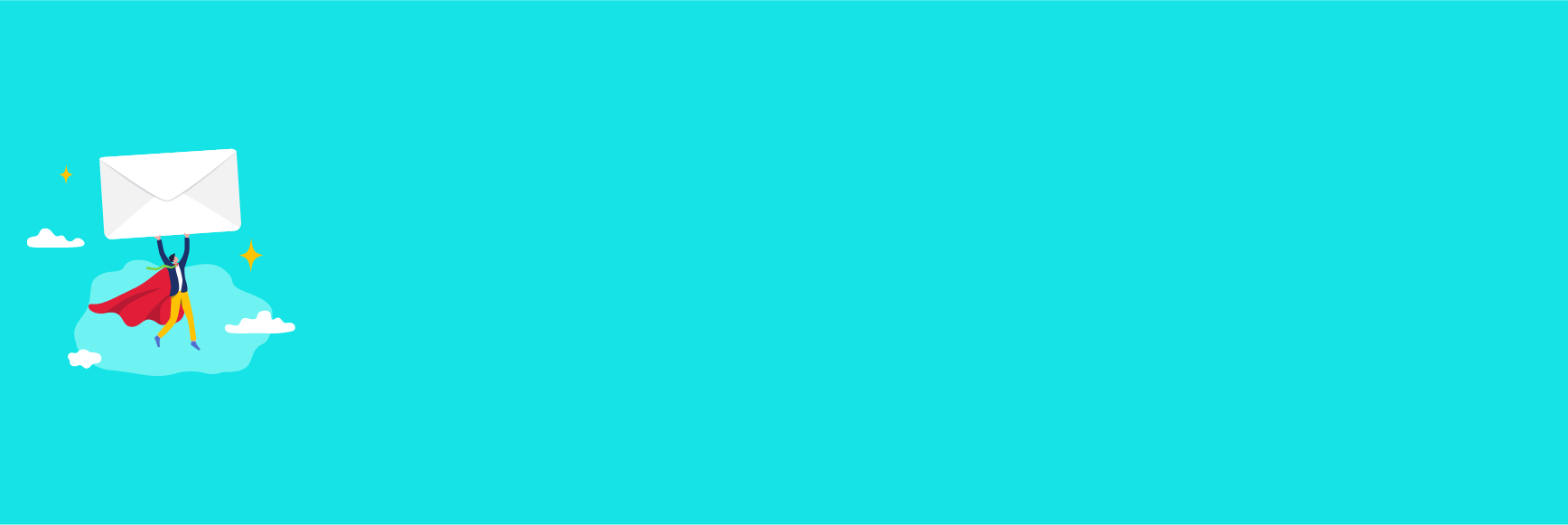
Be the First to Know
Subscribe to our monthly Pulse newsletter
to be the first to hear about new blog posts